A Look at the Post-Modern Compounding Facility (PMCF)
In June 2002, following a decision to re-centralize the production of Compounded Sterile Products (CSPs), the Advocate Illinois Masonic Medical Center of Chicago (AIMMC) formalized a strategic plan to redesign and upgrade its CSP facility. This modernization was to be carried out in order to assure compliance with the then-proposed USP <797> and other relevant industry standards to substantially improve the quality of AIMMC's sterile compounding processes.
As part of its ongoing IV Admixtures Quality Assurance Program for this institution, Lab Safety was asked to provide a comprehensive design which would assure compliance with the forthcoming Standard and it's likely revisions for the next decade. In order to re-centralize AIMMC's CSP production, the facility would need to provide ample workspace for the compounding and distribution/redistribution of a wide range of medium-risk CSPs.
Following a careful analysis of the intended work-streaming, waste-streaming, and personnel issues in the face of extreme space constraints, Lab Safety Corporation developed a new design approach which would facilitate efficient operation and accountability of AIMMC's expanding CSP operations. At the outset, it was determined that the quality of design/build operations would need to parallel those of a current cGMP facility design. Therefore, design, installation, operational, and performance qualifications of the PMCF would need to be carried out to meet the current and likely future requirements of USP <797>, ISO 14644, and current industry standards.
In September, 2002, the completed PMCF design was submitted by Lab Safety to AIMMC's Architectural and Engineering Staffs. Initially, considerable concern by these Departments was encountered due to the completely new, progressive, and inexpensive nature of the design. A continuous, sixteen-foot, ISO Class 4 (in-process) laminar-flow work-surface within an ISO Class 7 (in-process) core having double-pass-through pressure integrity interconnected with an ISO Class 8 (in-process) anteroom having single-pass-through pressure integrity, Class IIA Bio-Safety containment of antibiotics, and ample space for washing, gowning, staging, and preparation to be provided for an extremely low cost caused considerable skepticism.
In June 2003, following the Design Qualification (DQ) of the proposed facility, Power Construction, Inc., a Chicago area-based firm, was commissioned to build the PMCF.
Following completion of the build-out, Lab Safety Corporation commenced the Installation Qualification (IQ) to assure that all design components and equipment had been accurately and successfully installed in accordance with the DQ. The IQ was completed in February, 2004, with no exceptions noted.
In March 2004, following completion of the HVAC air balancing for the facility, the Operational Qualification (OQ) was completed by Lab Safety Corporation. With the exception of minor adjustments to the supply airflow and core pressurization, no additional operational corrections or repairs were required to produce operation of the facility and equipment in accordance with the DQ.
Review and certification of the DQ, IQ, and OQ phases of the PMCF validation were carried out, and the training of all CSP operatives was completed using the VALITEQ® Aseptic Technique Validation System. Upon completion of training, all operatives were successfully validated in the nine core aseptic techniques essential to all aseptic processes.
In addition, successful validation of the Containment/Aseptic Techniques of all operatives in the compounding of hazardous drugs was carried out by Lab Safety Corporation using the ChemoTEQ™ Containment/Aseptic Technique Validation System. All training and testing outcomes documented in the VALITEQ Documentation Management System (DMS) software and periodic re-validation activities were scheduled within the DMS.
As the final phase of the validation of the PMCF carried out subsequent to completion of the DQ, IQ, and OQ phases, the Performance Qualification (PQ) was represented as the combination of Individual Technique Validations, followed by a Complex Process Validation (i.e. a specific Process Validation was conducted to validate a complex dilution/syringe production procedure. In this procedure, SteriTEQ™ ST-50 concentrated growth media was reconstituted and substituted for actual drug product in a process simulation).
During this validation exercise performed in triplicate, each operative produced 250 syringe units under the most stressful conditions with an aggregate total of more than 1,500 units produced. No growth of any of the test subjects was observed, and the PQ was successfully accomplished. Representative samples of the simulated end-products were tested to confirm the viability of the test media. All positive controls demonstrated positive growth.
Synopsis
During his summary of the comprehensive pre-inspection review of the PMCF in July, 2004, Dr. Kenneth Hermann of the Joint Commission for Accreditation of Healthcare Organizations (JCAHO) made the assertion that the Post-Modern Compounding Facility at Advocate Illinois Masonic Medical Center was the first, fully-USP <797>-compliant facility he had ever seen. Dr. Hermann requested pictures of the facility in order to distribute these to other JCAHO inspectors for the purpose of demonstrating exactly how a fully-<797>-compliant facility should appear.
Testimonial
"At Advocate Illinois Masonic Medical Center Pharmacy, we have been using Lab Safety Corporation services for three years with excellent results. Lab Safety provided a design for a cleanroom/anteroom facility for our CSP preparation which is both USP <797> compliant, and conducive to an efficient operation. Using specific indicators for quality assurance, Lab Safety Corporation has also worked with us to establish a training program for our pharmacists and technicians to demonstrate competency in aseptic technique and compounding procedures. We also rely on their expertise in risk areas, such as chemotherapy preparation. Lab Safety's teaching materials are comprehensive and their staff is knowledgeable and easy to work with. I would highly recommend Lab Safety products and services for any hospital or facility that prepares CSP’s."
—Janet Jaramilla, PharmD., BCPS
Director of Pharmacy Services Advocate at Illinois Masonic Medical Center

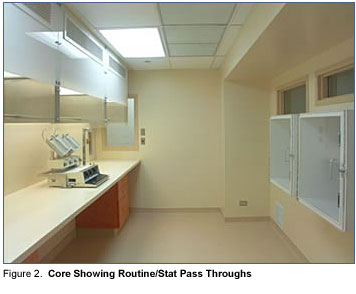
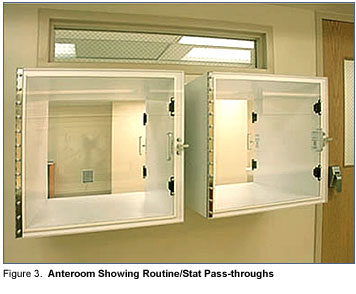
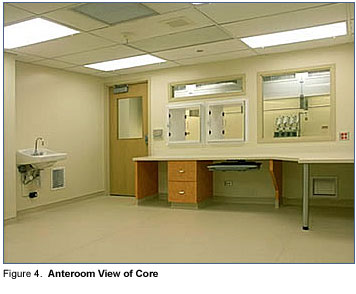
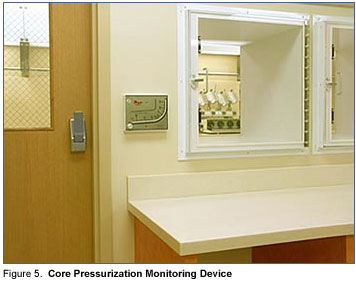
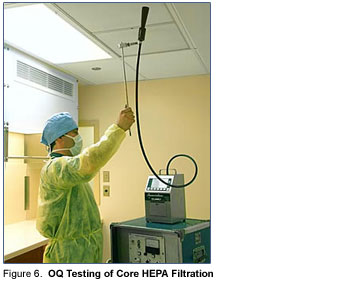
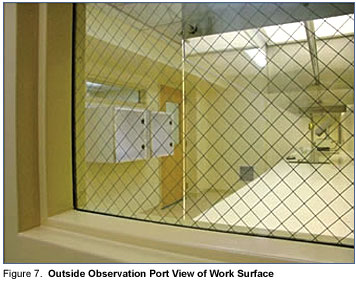